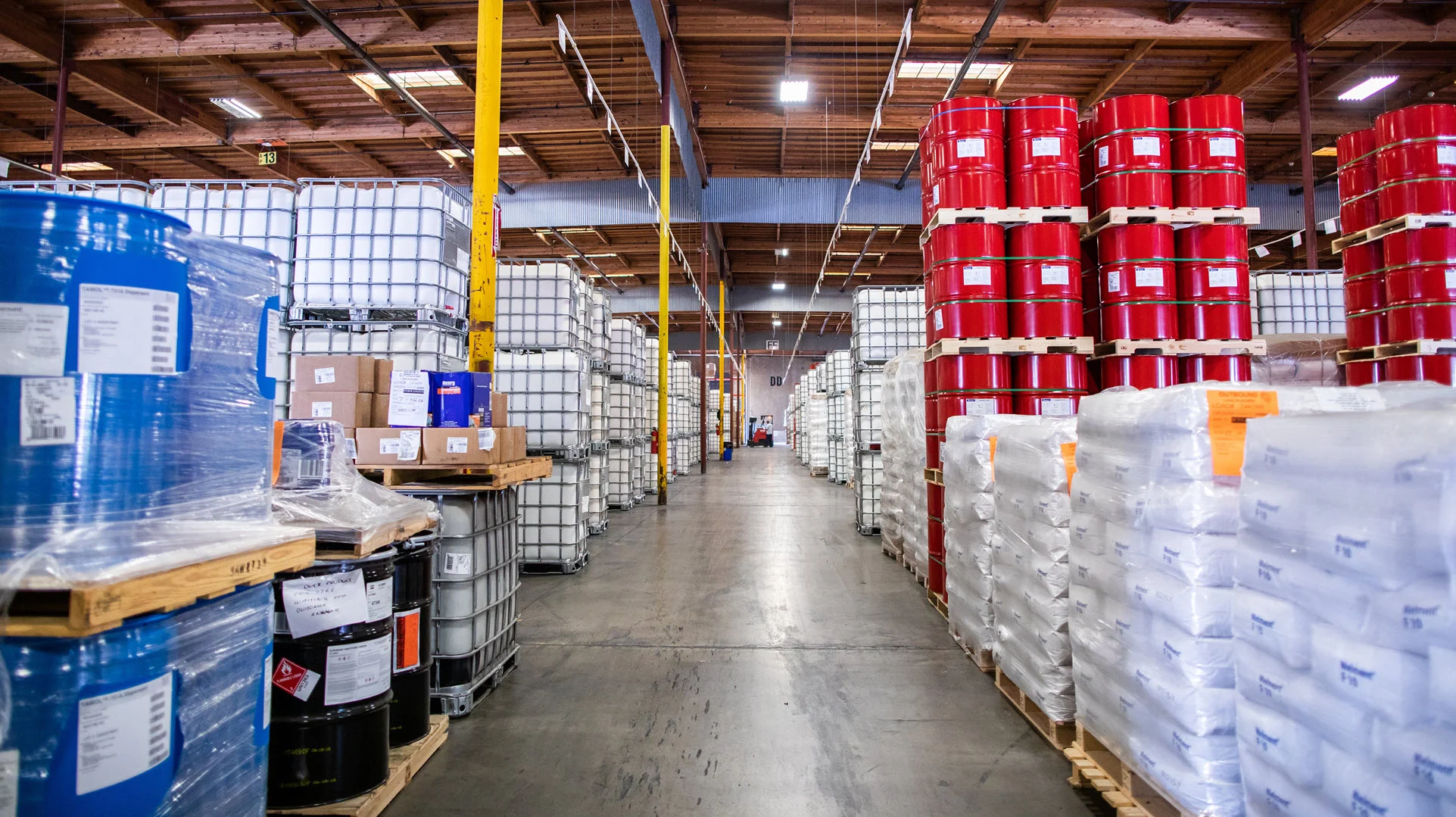
Chemicals play a significant role in various stages of footwear manufacturing, from the processing of raw materials to the final finishing of the product. Sulfur and accelerators are used to cross-link rubber molecules, improving its elasticity, strength, and durability. Many chemicals are added to plastics to increase their flexibility and workability during molding and shaping processes.
Pigments and dyes are used to color rubber and plastic components, such as outsoles and midsoles. A variety of adhesives, including solvent-based and water-based formulations, are used to bond different parts of the shoe, such as the upper to the sole. Protective coatings, such as polyurethane and acrylics, are applied to the upper and other components to enhance water resistance, abrasion resistance, and overall durability. Solvents like acetone and alcohol are used to clean and degrease various components during the manufacturing process. Wax based products are used to shine and protect the finished footwear.
While chemicals are essential for footwear manufacturing, it’s crucial to use them responsibly to minimize environmental impact and protect worker health. Storage is a vital part of the life cycle of these chemicals. Proper chemical storage is crucial for ensuring safety, preventing accidents, and maintaining environmental compliance.
Let’s discuss here some best practices for chemical storage in a manufacturing environment.
Segregation:
Separate incompatible chemicals to prevent hazardous reactions. Consider factors like reactivity, flammability, and corrosivity while storing chemicals together. Consult Safety Data Sheets (SDS) for specific compatibility information.
Ventilation:
Store chemicals in well-ventilated areas to minimize exposure to fumes. Use fume hoods for handling volatile or toxic chemicals.
Temperature Control:
Store chemicals within recommended temperature ranges to prevent degradation. Avoid extreme temperatures, especially for heat-sensitive or flammable substances.
Lighting:
Ensure adequate lighting to facilitate safe handling and identification.
Spill Containment:
Use spill containment trays or dykes to prevent spills from spreading. Have appropriate spill cleanup materials readily available.
Original Containers:
Store chemicals in their original containers with labels intact. Do not transfer chemicals to unmarked containers.
Labeling:
Clearly label containers with chemical name, hazard warnings, and concentration. Update labels as needed to reflect changes in contents.
Data Sheets:
Ensure Material Safety Data Sheets (MSDS) are available, understood and acted upon. Update MSDS as needed.
Container Integrity:
Regularly inspect containers for damage, leaks, or corrosion. Replace damaged containers promptly.
Storage Height:
Store heavy containers on lower shelves to reduce the risk of falls. Avoid overcrowding shelves.
Emergency Procedures:
Develop and implement emergency procedures for chemical spills, fires, and other accidents. Conduct regular training drills to ensure preparedness.
Emergency Equipment:
Have appropriate emergency equipment, such as fire extinguishers, eye wash stations, and safety showers, readily available.
Inventory Management:
Maintain an accurate inventory of chemicals to track usage and expiration dates. Dispose of expired or unwanted chemicals properly.
Training:
Provide regular training to employees on chemical safety, handling procedures, and emergency response.
Regulatory Compliance:
Adhere to all relevant local, state, and federal regulations regarding chemical storage and handling.
By following these best practices, we can significantly reduce the risks associated with chemical storage and create a safer working environment.