Footwear production involves a complex process of transforming and assembling components made from a variety of materials. The role of adhesives in shoemaking is paramount, as they are essential for achieving the desired shape and providing structural stability to the finished shoe.
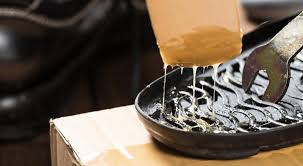
Adhesives are used to join the attaching the insole, midsole, and outsole. Adhesives help maintain the shoe’s shape and structural integrity. They provide support and stability, ensuring the shoe holds its form during wear and tear. Modern shoemaking often involves a variety of materials, such as leather, synthetic fabrics, rubber, and plastics. Adhesives are essential for creating strong and durable bonds between these diverse materials. The type of adhesive used can significantly impact the shoe’s flexibility and comfort. Certain adhesives allow for greater movement and bending, which is important for athletic shoes and other footwear designed for active lifestyles. Many shoe adhesives are formulated to be water-resistant, protecting the shoe’s interior from moisture and preventing damage.
Different type of adhesives are used in different operation in the footwear manufacturing process. Basically these can be divided in two major types as:
1. Rubber Based Adhesives
2. Polyurethane based adhesives
3. Hot Melt adhesives
Rubber Based adhesives
Rubber based adhesives can further be divided in three types:
Latex Based Adhesive
Natural Rubber Latex or Synthetic Rubber Latex is used in combining operations of different shoe components. Latex is widely used in combining different upper materials together such as Fabric, Leather, Synthetic Leather, Foam, EVA etc. It is also used in combining of Insole materials such as Insole board, Foam, Synthetic Leather etc. Latex is also used to join Rubber sole and foxing in Vulcanized shoes.
Rubber Based Solvent Adhesive
Natural or Synthetic Rubber dissolved in different solvents is also widely used in joining of shoe components specially where better bond strength is required than Latex.
Grafted Rubber Based Solvent Adhesive
Grafted Rubber dissolved in different solvents gives even better bond strength than the non-grafted Rubber adhesive. This type of adhesive is also widely used for Upper to Sole bonding where very high bond strength is not required.
Polyurethane Based Adhesive
There are two types of Polyurethane adhesives that are used in shoe making mainly in Upper to Sole Bonding.
Solvent Based PU Adhesive
Polyurethane Resin dissolved in different solvents is the most widely used adhesive used for Upper to Sole bond. This is a Transparent adhesive and needs a cross linking agent for improved performance. Usually this adhesive has 16-20 % solid content for brush application. PU adhesive, when applied to shoe components require makes a layer on the component and once the solvent evaporated this layer becomes dry. This layer needs to be activated so as it can develop a tack and can stick to the other component. The activation is done by flash heating the component at 80° C for a few seconds. Solvent based PU adhesives give the best bond strength of all shoe making adhesives. The bond remains flexible and due to crosslinker it also has good water resistance and thermal stability.
Water Based Polyurethane Adhesives
Water based Polyurethane adhesives comprise of a suspension of PU resin in water. These adhesives usually have 40 to 50 % resin content. These are white in color but after drying the film becomes transparent. These adhesives are a greener alternative to the solvent based adhesives with marginally lower bond strength. This type of adhesive needs forced drying as water needs to be evaporated at much higher temperature as compared to solvents. The application process is similar to solvent based adhesives with activation required to develop tag in the film after drying. Water resistance of these adhesives is somewhat less than the solvent based counter parts.
Hot-Melt Adhesives
Hot melt adhesives (HMAs) have become a popular choice in shoe manufacturing due to their numerous advantages. HMAs are solid adhesives that are melted into a liquid state before being applied. They solidify upon cooling, forming a strong bond. Common types used in shoemaking include EVA (ethylene-vinyl acetate), Polyamide (PA), and Polyurethane (PUR). HMAs set quickly, enabling faster production times. They can bond a wide range of materials used in shoe construction, including leather, textiles, rubber, and plastics. • HMA application can be easily automated, increasing efficiency and consistency. Many HMAs are solvent-free, reducing environmental impact.
Typical Applications in Shoemaking
• Sole Attachment: Bonding the outsole, midsole, and insole to the upper.
• Upper Assembly: Joining various components of the shoe upper, such as the vamp, quarter, and tongue.
• Reinforcement: Adding reinforcement patches or overlays for added durability.
• Decorative Elements: Applying decorative trims or accents.